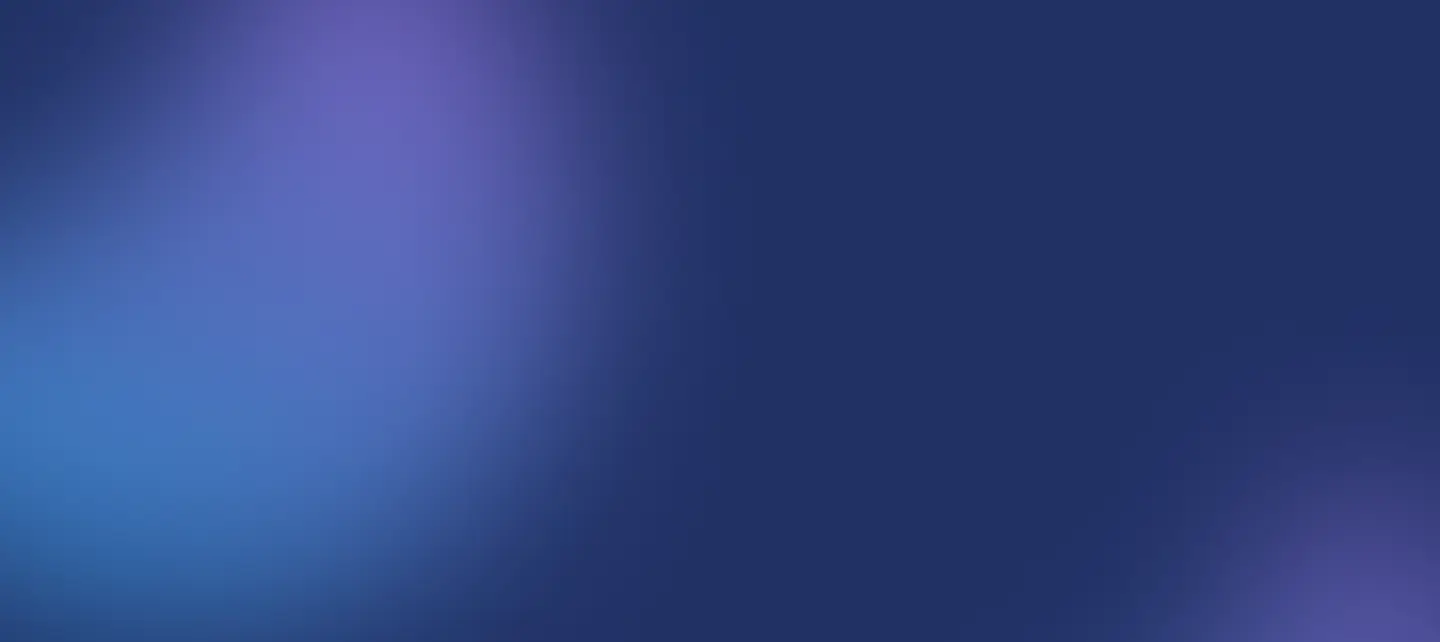
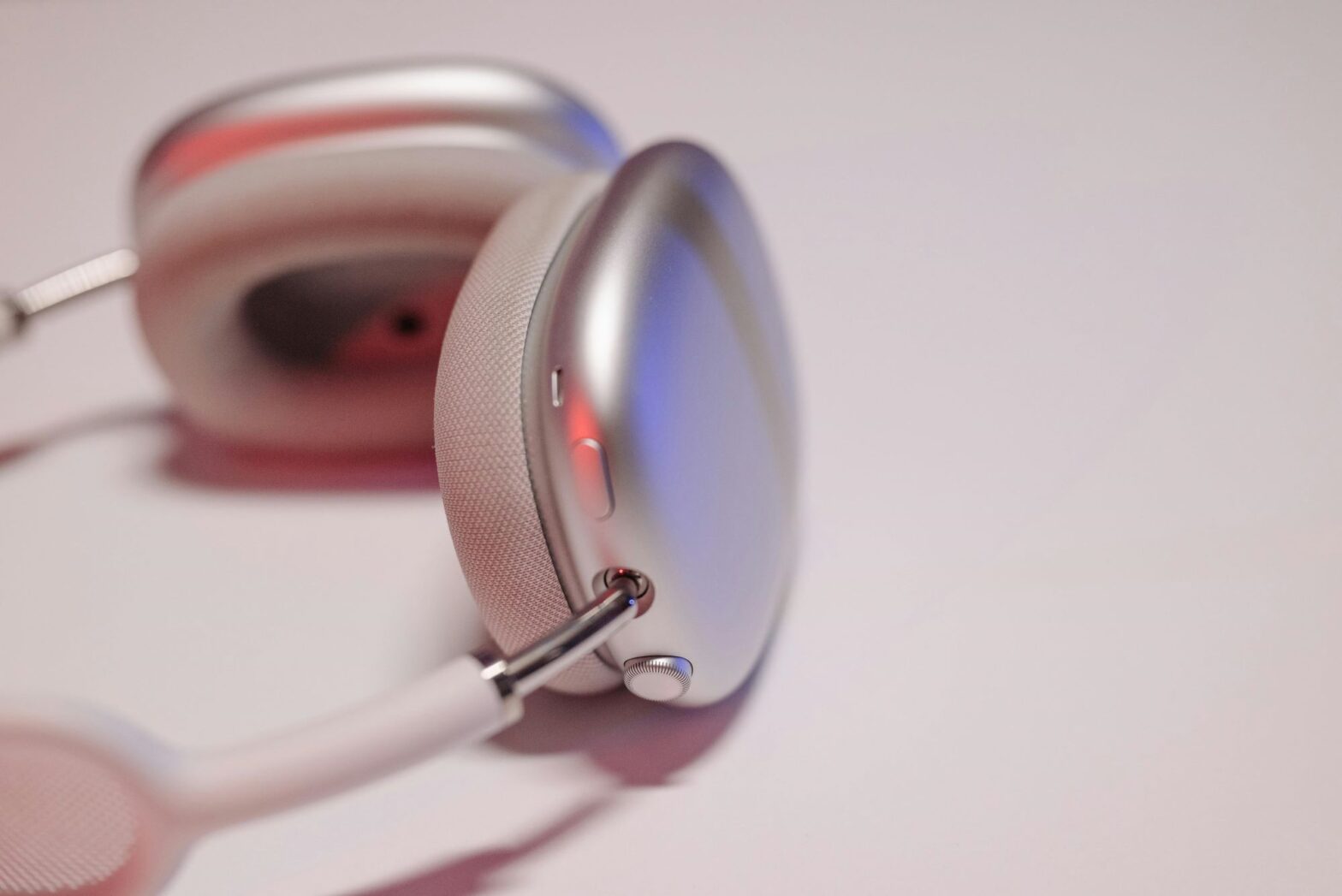
Electropolishing: Unveiling the Secrets Behind Shiny Metal Surfaces
Electropolishing, also known as electrochemical polishing or electro-smoothing, is an innovative process used for surface treatment of metal parts. This technology, often referred to as electropolishing in English, not only creates a shiny finish but also enhances the properties and durability of metal components. In industrial manufacturing, electropolishing plays a crucial role as it offers a high degree of precision and aesthetic appeal. But what exactly happens in this process, and why is it gaining importance in practice? Let’s explore the fascinating secrets that make electropolishing an indispensable tool in modern metalworking.
Fundamentals of Electropolishing: An Overview
To develop a deeper understanding of electropolishing, we must first look at the electrochemical principles behind this technique. In electropolishing, the metal piece to be treated is immersed in a specially designed polishing solution, which acts as an electrolyte. In this electrochemical system, the workpiece serves as the anode, and the application of direct current is essential to achieve the desired effects. The anodization process causes ionization of the uneven metal surfaces, which begin to dissolve in controlled layers.
This process significantly reduces surface roughness, giving the metal a smoother and more uniform surface. One of the key strengths of electropolishing is its ability to remove microscopic imperfections that often remain after mechanical polishing and can affect the surface integrity. Electropolishing techniques provide a remarkable improvement in this integrity. However, there is now a new alternative to electropolishing that promises similar results.
Electropolishing is particularly effective with materials such as stainless steel, aluminum, copper, and titanium. Yet, its flexibility and adaptability allow it to be applied to many alloyed metals, greatly expanding its range of applications.
Beyond its aesthetic enhancement, electropolishing is invaluable in hygienically sensitive industries. In sectors such as medical technology, food processing, and pharmaceuticals, there is a high demand for flawless surfaces, as they minimize the accumulation of bacteria and microorganisms. The removal of tiny material layers reduces the risk of microscopic cracks and pores, making the resulting surfaces easier to clean and more hygienic. Thus, electropolishing plays a crucial role in meeting hygiene standards and ensuring product purity.
Applications in Various Industries
Electropolishing has extended its application far beyond simply creating shiny surfaces, becoming an integral part of numerous key industries. In medical technology, for example, this process is of immense value. Surgical instruments must not only be precise and functional but also exhibit extremely smooth surfaces to drastically reduce the risk of infections. These smooth surfaces are less likely to attract organic residues and offer higher resistance to harsh chemicals, enhancing their durability and safety.
In the automotive and aerospace industries, electropolishing is just as indispensable. Here, it is not only about design but also about functional improvements such as weight reduction and performance enhancement. Electropolished components help reduce air and flow resistance due to their improved surface structure, ultimately increasing vehicle efficiency. Additionally, in the production of electronics and catalysts, electropolished metal surfaces are important for improving electrical conductivity and the efficiency of catalysts.
The food and beverage industry also greatly benefits from electropolishing. It ensures that storage tanks, pipelines, and containers remain clean and corrosion-resistant. Such surfaces prevent contamination buildup, which is essential for adhering to the purity requirements in these sectors.
Jewelry and high-end consumer goods also profit from electropolishing. Alongside the outstanding aesthetics that these shiny surfaces provide, the process also increases the durability and scratch resistance of the products. It has a significant impact on the luxury market by helping to create products with a flawless, premium finish that meets the highest standards of quality. In this way, electropolishing uniquely combines functionality with exclusive visual appeal.
Advantages Over Traditional Polishing Methods
Compared to traditional mechanical or chemical polishing processes, electropolishing offers many advantages, making it the preferred choice in numerous industrial applications. One of the primary benefits of electropolishing is its exceptional ability to significantly improve the roughness and microstructure of metal surfaces. Mechanical polishing methods tend to yield inconsistent results, particularly with complex geometries. In contrast, electropolishing ensures uniform and precise treatment of the entire surface.
Moreover, electropolishing offers the significant advantage of reducing internal stresses that may arise during the manufacturing or shaping of metal parts. These stresses can negatively impact the mechanical strength and durability of a workpiece. By selectively removing material layers, electropolishing reduces these stresses, improving the structural integrity of the treated part.
The process is also more environmentally friendly than many other surface treatment methods. By minimizing abrasive and chemical residues, it generates less waste, and the need for cleaning agents and energy is reduced. This leads to a sustainable and eco-conscious approach to surface treatment.
Another significant advantage of electropolishing lies in the reproducibility and consistency of the results. The use of electronic control and monitoring mechanisms during the process ensures that the high quality of the treated parts is maintained. This consistency makes electropolishing particularly valuable for mass production, where even slight deviations can negatively affect overall product quality. Thus, electropolishing not only contributes to the production of high-quality products but also to more efficient and cost-effective production processes.
Challenges and Considerations in Electropolishing
Despite the numerous advantages and growing popularity of electropolishing, there are some challenges and important considerations that companies must address to achieve the best results. One of the most significant challenges lies in the preparation of the workpiece. In addition to thorough cleaning to remove contaminants like oils, greases, or oxidized layers, attention must also be paid to the metal’s surface itself. Poor preparation can result in irregularities during treatment, leading to undesirable outcomes and increased costs.
Additionally, controlling the process parameters is crucial. Proper regulation of voltage, current, and the composition of the polishing solution is essential. Each of these elements must be precisely adjusted to ensure positive results. Incorrect settings can lead to poor polishing quality or even damage to the surface, such as etching or defects. This requires skilled professionals and a solid understanding of electrochemical processes to ensure that all parameters are optimally set.
The disposal of electrolyte solutions also presents a challenge. Although electropolishing leaves behind fewer abrasive residues than traditional mechanical methods, the solutions used often contain environmentally harmful chemicals. Therefore, proper and eco-friendly disposal is essential to minimize the process’s ecological footprint. It is important to develop and implement efficient and sustainable disposal methods to reduce environmental impact.
Another consideration is cost. Electropolishing is often more expensive than traditional polishing methods, especially for smaller production runs. This is mainly due to the specialized equipment and materials required for the process. Therefore, companies should carefully weigh whether the surface quality improvement justifies the additional cost. Particularly in large-scale productions, increased investments can be offset by efficiency gains and the quality of the end products. Ultimately, employing electropolishing requires a thorough cost-benefit analysis to determine whether this technology is the right choice for specific applications.
The Future of Electropolishing in Modern Industry
As technologies and industrial processes continue to evolve, the importance of electropolishing is increasing significantly. This technique surpasses many traditional manufacturing methods in its adaptability, allowing it to integrate seamlessly into existing production workflows. This opens up countless possibilities for innovation and experimentation in manufacturing technology. Modern industries are increasingly demanding products that are both functionally and aesthetically outstanding. In this regard, electropolishing proves to be an indispensable tool to meet these demands.
An exciting area of research focuses on advanced computer-aided analysis software aimed at improving electropolishing processes. Engineers can use these technologies to simulate the optimal parameters for the process, leading to more efficient and effective implementation. In parallel, intensive research is being conducted into new, environmentally friendly electrolyte solutions. These developments are aimed at making the electropolishing process more sustainable by minimizing harmful residues and enabling the use of more eco-friendly materials.
Furthermore, combining electropolishing with other modern manufacturing techniques, such as 3D printing, holds promising potential. 3D-printed metal parts tend to have slight surface irregularities that can be significantly smoothed by electropolishing. This synergy offers new perspectives for manufacturing parts that come directly from the printer and meet high precision and surface smoothness standards.
In conclusion, electropolishing goes far beyond just creating shiny surfaces. It impressively combines precision, aesthetics, and functionality, setting new standards in manufacturing. The technology is strategically positioning itself as a driving force in the future design of products across many industries, offering numerous possibilities for customization through technological advancements and environmentally friendly practices.
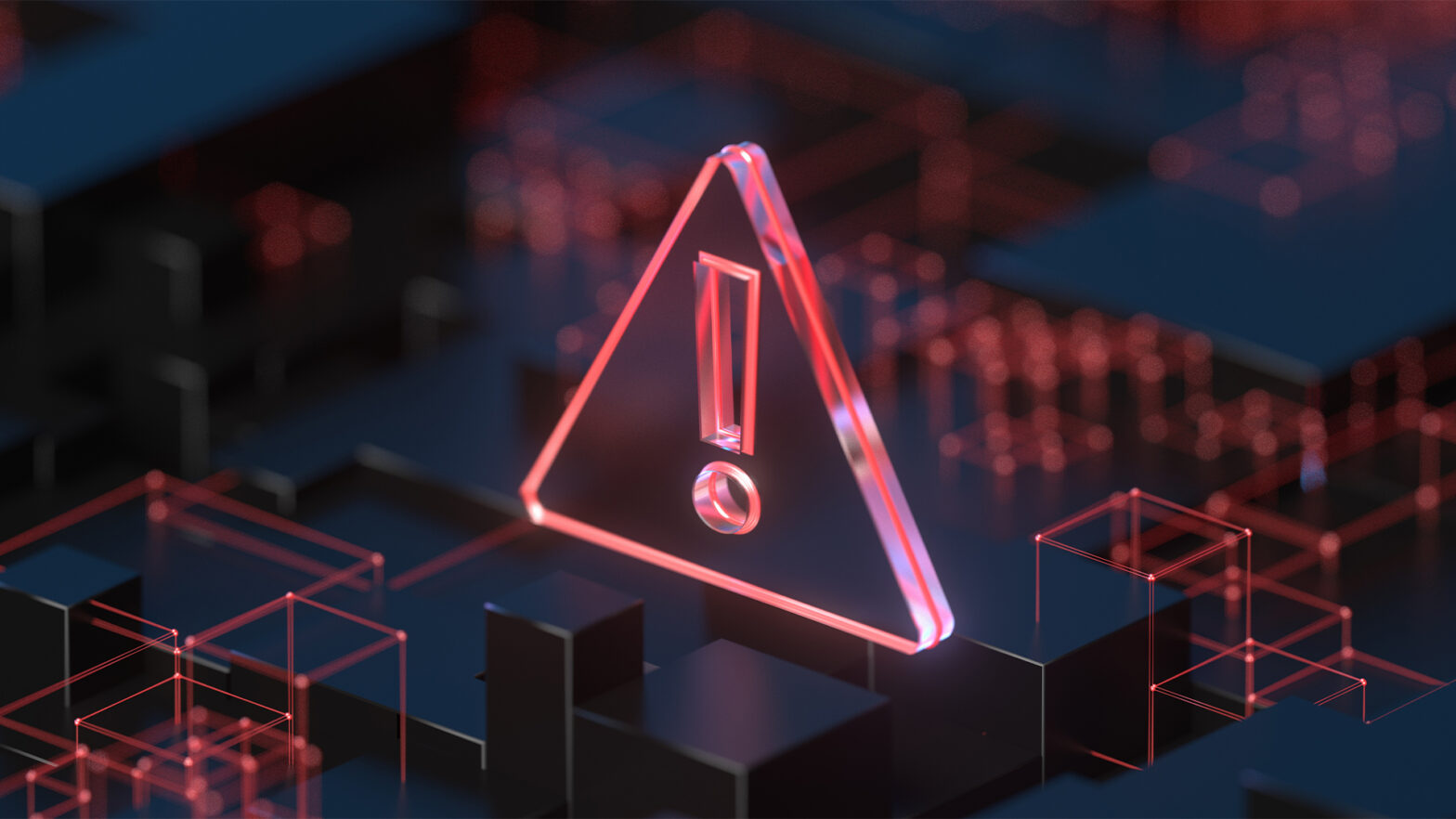
Technology
25 March 2025
Ransomware-As-A-Service Variants on the Rise With Critical Infrastructure Providers at the Greatest Risk
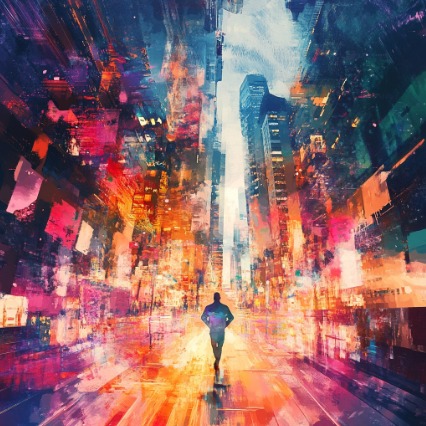
Business Advice
25 March 2025
Claims Processing Automation: How Insurers Can Cut Costs and Improve CX
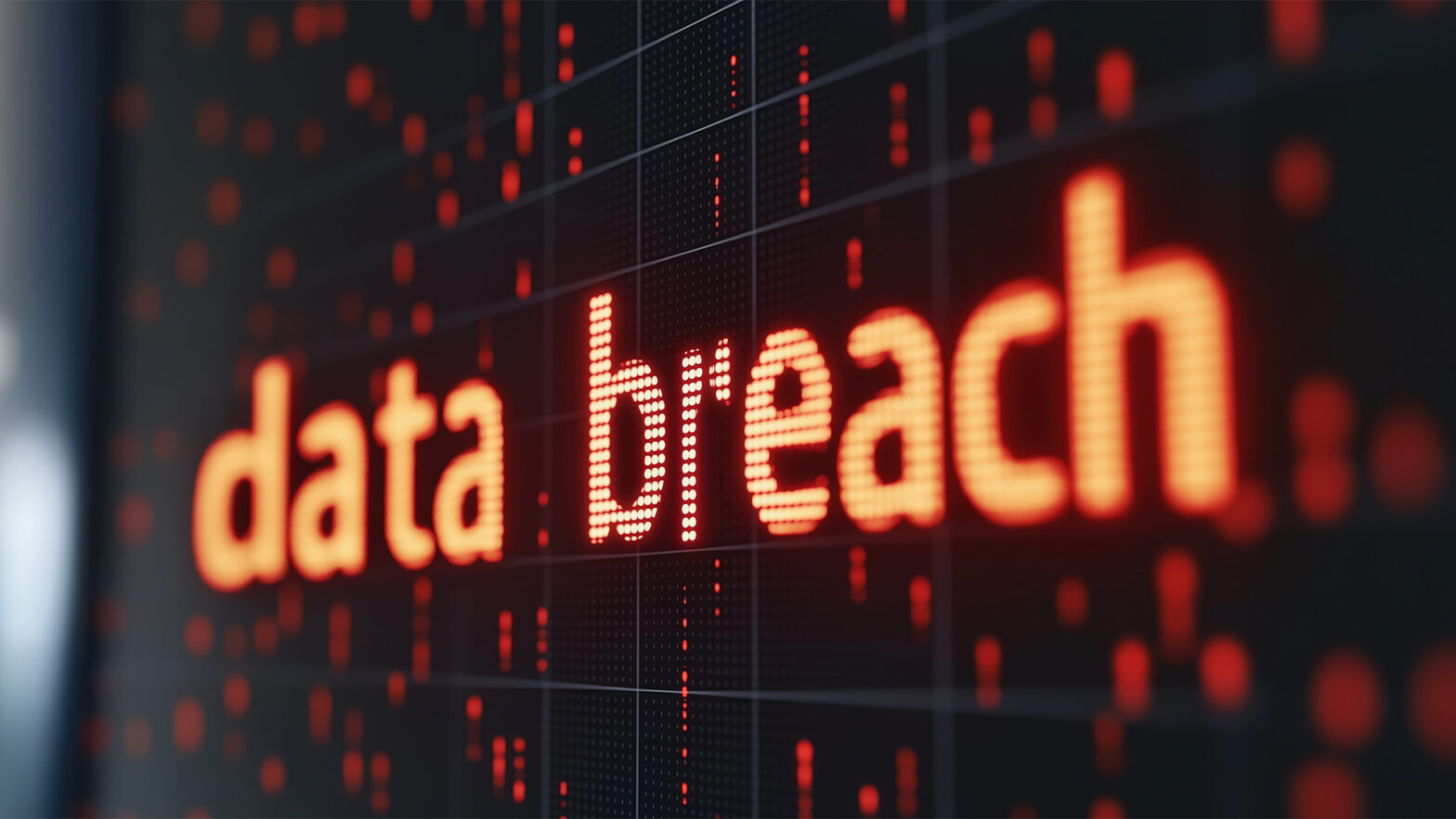
Technology
18 March 2025
Secret Signs Your Internet Security Has Been Compromised